Resumes
Resumes
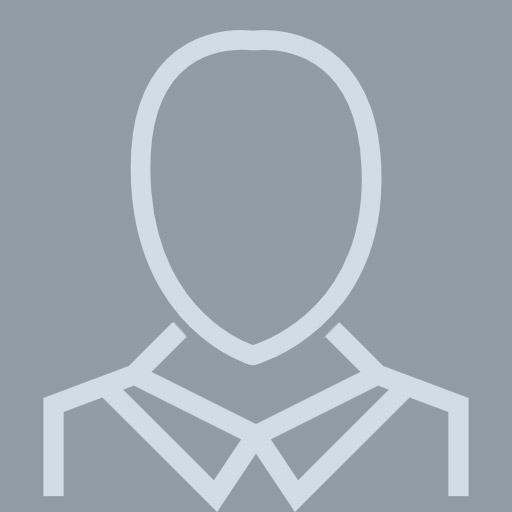
Director, Npi Engineering
View pageLocation:
600 Hudson Dr, Santa Clara, CA 95051
Industry:
Medical Devices
Work:
Intuitive Surgical - Sunnyvale,CA since Aug 2012
NPI manager, Instruments
Intuitive Surgical since Aug 2010
Sr. Manufacturing Engineer
St. Jude Medical - CRMD Aug 2006 - May 2009
Hardware Design Engineer
Applied Materials Aug 2004 - Aug 2006
Mechanical Engineer
Stanford University Sep 2003 - Jun 2004
Teaching Assistant
NPI manager, Instruments
Intuitive Surgical since Aug 2010
Sr. Manufacturing Engineer
St. Jude Medical - CRMD Aug 2006 - May 2009
Hardware Design Engineer
Applied Materials Aug 2004 - Aug 2006
Mechanical Engineer
Stanford University Sep 2003 - Jun 2004
Teaching Assistant
Education:
Stanford University
M.S, Mechanical Engineering
M.S, Mechanical Engineering
Skills:
Medical Devices
Product Development
Cross Functional Team Leadership
Manufacturing
Design Control
Engineering
R&D
Design of Experiments
Project Management
Product Design
Design For Manufacturing
Failure Mode and Effects Analysis
Leadership
Management
Fmea
Iso 13485
Research and Development
Validation
Product Development
Cross Functional Team Leadership
Manufacturing
Design Control
Engineering
R&D
Design of Experiments
Project Management
Product Design
Design For Manufacturing
Failure Mode and Effects Analysis
Leadership
Management
Fmea
Iso 13485
Research and Development
Validation
Languages:
English