Resumes
Resumes

Professor Emeritus
View pageLocation:
206 18Th Ave west, Columbus, OH 43210
Industry:
Automotive
Work:
The Ohio State University since Jan 1986
Professor
OSU Center For Automotive Research since 1986
Professor
FloCoTec, Inc 1990 - 1996
Founder and Chief Scientist
Professor
OSU Center For Automotive Research since 1986
Professor
FloCoTec, Inc 1990 - 1996
Founder and Chief Scientist
Education:
Illinois Institute of Technology 1980 - 1985
PhD, Mechanical and Aerospace Engineering Institut national des Sciences appliquées de Lyon 1974 - 1979
Diplome d'ingenieur, Genie Mechanique Construction (GMC)
PhD, Mechanical and Aerospace Engineering Institut national des Sciences appliquées de Lyon 1974 - 1979
Diplome d'ingenieur, Genie Mechanique Construction (GMC)
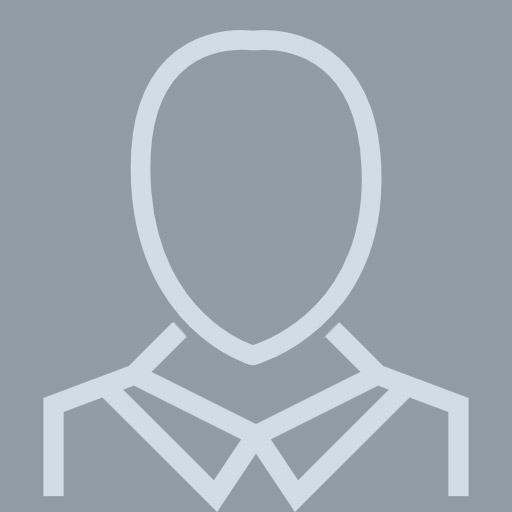
Professor At The Ohio State University
View pageLocation:
Columbus, OH
Industry:
Higher Education
Work:
The Ohio State University
Professor at the Ohio State University
Professor at the Ohio State University