Resumes
Resumes
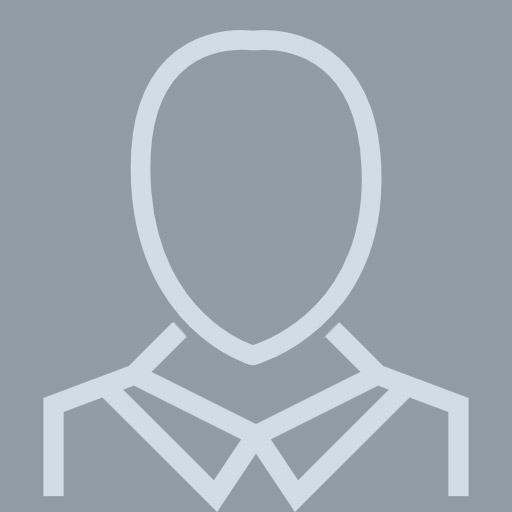
William Collan Clarksburg, NJ
View pageWork:
Computerized Elevator Controls
Moonachie, NJ
Oct 2012 to Feb 2014
Senior Embedded Software Engineer; Contractor
Redaptive Technologies LLC
Township of Warren, NJ
Mar 2009 to Oct 2012
Principal Developer
PolyType America
Mahwah, NJ
Nov 2008 to Mar 2009
Inkjet Controls Specialist/Senior Developer
Leggett & Platt Digital Technologies
Somerset, NJ
Feb 1998 to Nov 2008
Lead Developer
Pathe Technologies
Irvington, NJ
May 1996 to Feb 1998
Lead Developer
Self-Employed
Monroe, NY
Jul 1986 to May 1996
Consultant
HF Henderson Industries
W Caldwell, NJ
Jun 1980 to Jul 1986
Project Engineer/ Programmer
Moonachie, NJ
Oct 2012 to Feb 2014
Senior Embedded Software Engineer; Contractor
Redaptive Technologies LLC
Township of Warren, NJ
Mar 2009 to Oct 2012
Principal Developer
PolyType America
Mahwah, NJ
Nov 2008 to Mar 2009
Inkjet Controls Specialist/Senior Developer
Leggett & Platt Digital Technologies
Somerset, NJ
Feb 1998 to Nov 2008
Lead Developer
Pathe Technologies
Irvington, NJ
May 1996 to Feb 1998
Lead Developer
Self-Employed
Monroe, NY
Jul 1986 to May 1996
Consultant
HF Henderson Industries
W Caldwell, NJ
Jun 1980 to Jul 1986
Project Engineer/ Programmer
Education:
Stevens Institute of Technology
Hoboken, NJ
1976 to 1980
Bachelor of Engineering
Hoboken, NJ
1976 to 1980
Bachelor of Engineering