Resumes
Resumes
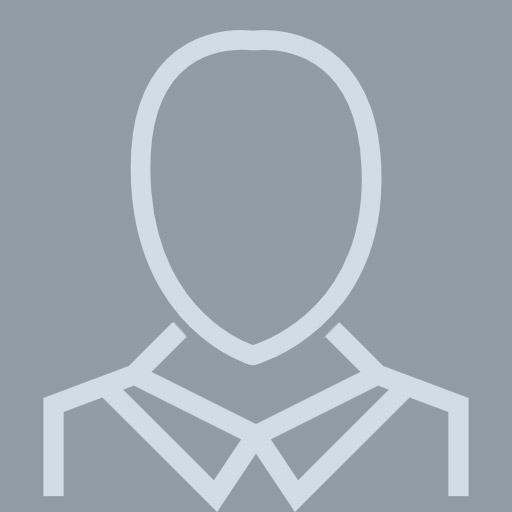
Vice President
View pageLocation:
4468 Piper Dr, San Jose, CA 95129
Industry:
Semiconductors
Work:
Anst
Vice President
Syp Aug 2017 - Mar 2019
Senior Director, Ald Technology
Intermolecular Aug 2011 - Apr 2017
Senior Member of Technical Staff and Senior Manager of Technical Transfer
Applied Materials Oct 2008 - Jul 2011
Gpm and Manager, Solar Technology
Novellus Systems Sep 1, 2000 - Oct 1, 2008
Senior Process Engineer and Key Account Technologist
Vice President
Syp Aug 2017 - Mar 2019
Senior Director, Ald Technology
Intermolecular Aug 2011 - Apr 2017
Senior Member of Technical Staff and Senior Manager of Technical Transfer
Applied Materials Oct 2008 - Jul 2011
Gpm and Manager, Solar Technology
Novellus Systems Sep 1, 2000 - Oct 1, 2008
Senior Process Engineer and Key Account Technologist
Education:
University of Idaho 1993 - 1997
Doctorates, Doctor of Philosophy, Metallurgical Engineering University of Science and Technology Beijing 1984 - 1987
Master of Science, Masters, Metallurgical Engineering
Doctorates, Doctor of Philosophy, Metallurgical Engineering University of Science and Technology Beijing 1984 - 1987
Master of Science, Masters, Metallurgical Engineering
Skills:
Thin Films
Semiconductors
Semiconductor Industry
Cvd
R&D
Silicon
Design of Experiments
Jmp
Pvd
Characterization
Solar Energy
Pecvd
Failure Analysis
Materials Science
Metrology
Solar Cells
Process Integration
Research and Development
Physical Vapor Deposition
Plasma Physics
Atomic Layer Deposition
Chemical Vapor Deposition
Photolithography
Ald
Semiconductor Process
Etching
Plasma Enhanced Chemical Vapor Deposition
Semiconductors
Semiconductor Industry
Cvd
R&D
Silicon
Design of Experiments
Jmp
Pvd
Characterization
Solar Energy
Pecvd
Failure Analysis
Materials Science
Metrology
Solar Cells
Process Integration
Research and Development
Physical Vapor Deposition
Plasma Physics
Atomic Layer Deposition
Chemical Vapor Deposition
Photolithography
Ald
Semiconductor Process
Etching
Plasma Enhanced Chemical Vapor Deposition
Languages:
Mandarin
English
English
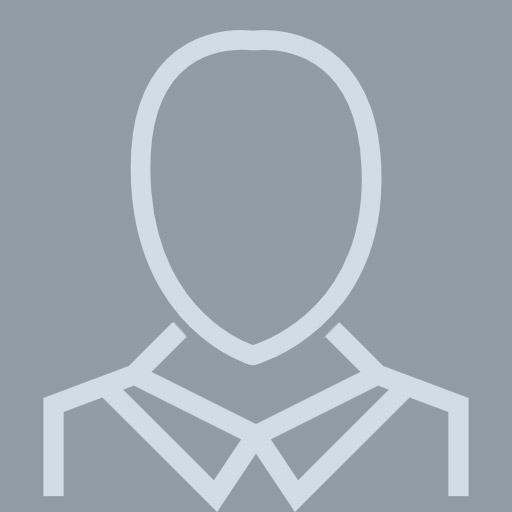