Resumes
Resumes
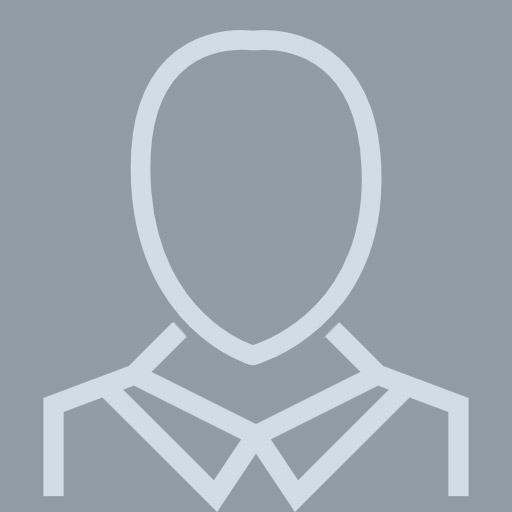
President
View pageLocation:
Knoxville, TN
Industry:
Mining & Metals
Work:
Alcoa
Carbon Plant, Furnace, and Asset Integrity Specialist
Lockwood Greene 2000 - 2005
Project Engineer
Manufacturing Sciences Corporation 1995 - 2000
Project Manager
Alcoa 1988 - 1995
Senior Mechanical Engineer-Major Projects, Maintenance Supervisor
Macnair Solutions 1988 - 1995
President
Carbon Plant, Furnace, and Asset Integrity Specialist
Lockwood Greene 2000 - 2005
Project Engineer
Manufacturing Sciences Corporation 1995 - 2000
Project Manager
Alcoa 1988 - 1995
Senior Mechanical Engineer-Major Projects, Maintenance Supervisor
Macnair Solutions 1988 - 1995
President
Education:
Georgia Institute of Technology 1982 - 1988
Bachelors, Bachelor of Science, Mechanical Engineering Campbell High School
Georgia Tech
Bachelors, Bachelor of Science, Mechanical Engineering Campbell High School
Georgia Tech
Skills:
Engineering
Preventive Maintenance
Continuous Improvement
Aluminum
Commissioning
Reliability Engineering
Factory
Root Cause Analysis
Materials
Project Engineering
Mining
Mechanical Engineering
Maintenance Management
Procurement
Combustion Systems
Metals
Automation
Construction
Aluminum Manufacturing
Preventive Maintenance
Continuous Improvement
Aluminum
Commissioning
Reliability Engineering
Factory
Root Cause Analysis
Materials
Project Engineering
Mining
Mechanical Engineering
Maintenance Management
Procurement
Combustion Systems
Metals
Automation
Construction
Aluminum Manufacturing