Resumes
Resumes
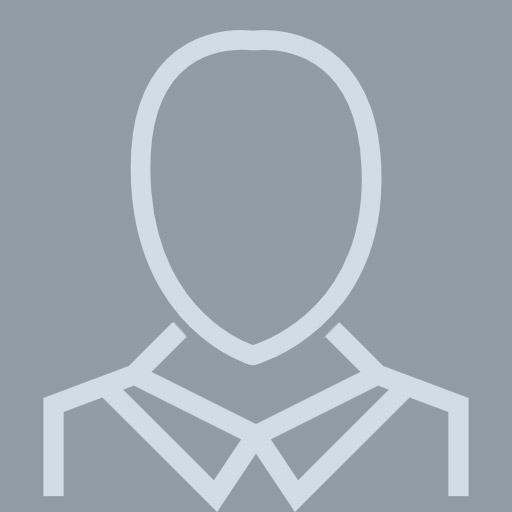
Vadim Daskal
View pageLocation:
Columbus, OH
Industry:
Medical Devices
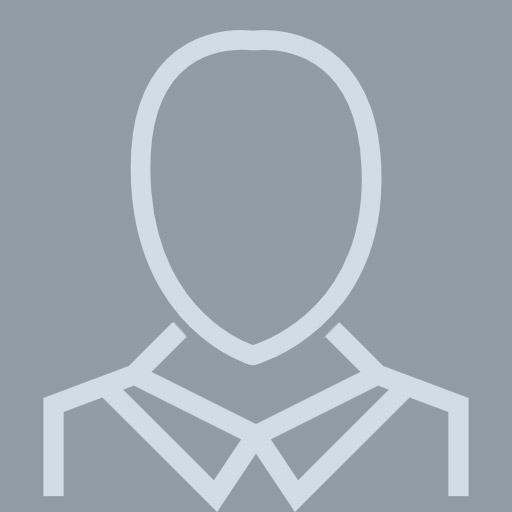
Art Director, Owner At Papelcouture
View pagePosition:
Art Director, owner at Papelcouture, Owner at LCS (Laser Cutting Shapes)
Location:
Columbus, Ohio Area
Industry:
Design
Work:
Papelcouture - Columbus, Ohio Area since Jan 2011
Art Director, owner
LCS (Laser Cutting Shapes) since Jul 2008
Owner
Boston Lasers Jun 2004 - Feb 2008
Owner
BD Jul 2001 - Apr 2004
Sr. Process Development Engineer
3M Mar 1998 - Jul 2001
Sr. Process Development Engineer
Art Director, owner
LCS (Laser Cutting Shapes) since Jul 2008
Owner
Boston Lasers Jun 2004 - Feb 2008
Owner
BD Jul 2001 - Apr 2004
Sr. Process Development Engineer
3M Mar 1998 - Jul 2001
Sr. Process Development Engineer
Education:
Odessa State Academy of Refrigeration
ms, Refrigeration technology
ms, Refrigeration technology
Interests:
Laser cutting services: wood, fabric, textile, plastic, avrylic, paper, cardboard