Resumes
Resumes
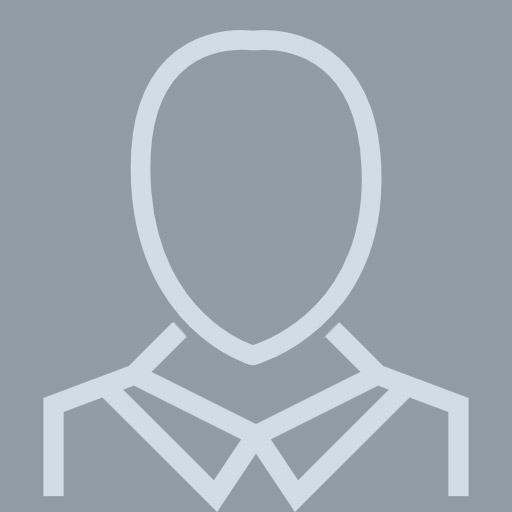
Associate Professor
View pageLocation:
62 Beal Dr, Southington, CT 06489
Industry:
Research
Work:
University of Connecticut, Department of Chemistry since 2004
Associate Professor
Chemical Innovations Institute - Farmington, CT since Sep 2012
Interim Director
Calvary Fellowship (West Hartford) since 2006
Serving Coordinator
King's College London 1999 - 2004
Lecturer
Associate Professor
Chemical Innovations Institute - Farmington, CT since Sep 2012
Interim Director
Calvary Fellowship (West Hartford) since 2006
Serving Coordinator
King's College London 1999 - 2004
Lecturer
Education:
University of Cambridge 1993 - 1996
Ph.D., Chemistry
Ph.D., Chemistry
Skills:
Chemistry
Organic Chemistry
Organic Synthesis
Laboratory
Research
Nmr
Product Development
Lifesciences
Organic Chemistry
Organic Synthesis
Laboratory
Research
Nmr
Product Development
Lifesciences