Resumes
Resumes
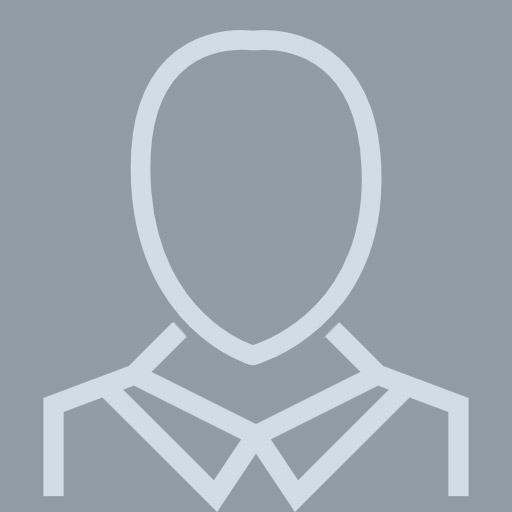
Senior Systems Engineer
View pageLocation:
22118 41St Pl south, Kent, WA 98032
Industry:
Aviation & Aerospace
Work:
Mitsubishi Electric Research Labs - Cambridge, MA since Jul 2009
Member Research Staff
University of Connecticut - Storrs, CT Aug 2005 - Jun 2009
Research Assistant
SolidWorks-CADCAMCIM Inc. - Waltham, MA Dec 2008 - Jan 2009
Software Engineer Intern
SolidWorks-CADCAMCIM Inc. - Waltham, MA May 2008 - Aug 2008
Software Engineer Intern
Delft University of Technology - Delft Area, Netherlands May 2007 - Aug 2007
Visiting Researcher
Member Research Staff
University of Connecticut - Storrs, CT Aug 2005 - Jun 2009
Research Assistant
SolidWorks-CADCAMCIM Inc. - Waltham, MA Dec 2008 - Jan 2009
Software Engineer Intern
SolidWorks-CADCAMCIM Inc. - Waltham, MA May 2008 - Aug 2008
Software Engineer Intern
Delft University of Technology - Delft Area, Netherlands May 2007 - Aug 2007
Visiting Researcher
Education:
The University of Connecticut 2005 - 2009
KoƧ University 2003 - 2005
Middle East Technical University 2000 - 2003
KoƧ University 2003 - 2005
Middle East Technical University 2000 - 2003
Skills:
Simulations
Optimization
Matlab
Numerical Analysis
R&D
Algorithms
Cad/Cam
Machining
Computational Geometry
Programming
C++
Mathematical Modeling
Robotics
Python
Solid Modeling
Software Development
Simulink
Composites
Engineering
Composite Manufacturing
Systems Engineering
Additive Manufacturing
Teamwork
Product Development
Leadership
Cross Functional Team Leadership
Analytical Skills
Optimization
Matlab
Numerical Analysis
R&D
Algorithms
Cad/Cam
Machining
Computational Geometry
Programming
C++
Mathematical Modeling
Robotics
Python
Solid Modeling
Software Development
Simulink
Composites
Engineering
Composite Manufacturing
Systems Engineering
Additive Manufacturing
Teamwork
Product Development
Leadership
Cross Functional Team Leadership
Analytical Skills
Languages:
English
Japanese
Turkish
Japanese
Turkish