Resumes
Resumes
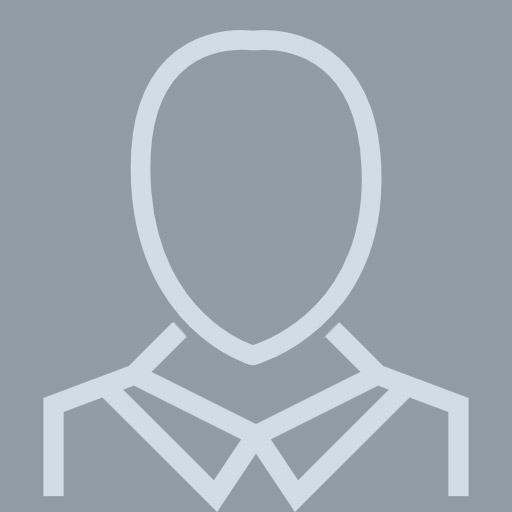
Chief Technical Officer
View pageLocation:
25639 Deep Creek Blvd, Punta Gorda, FL 33983
Industry:
Machinery
Work:
Agr International Inc Mar 2001 - Aug 2010
Director of Engineering
Agr International Inc Mar 2001 - Aug 2010
Chief Technical Officer
Director of Engineering
Agr International Inc Mar 2001 - Aug 2010
Chief Technical Officer
Skills:
Technology Management
Product Development
Cross Functional Team Leadership
Process Engineering
Engineering
Continuous Improvement
Software Engineering
Manufacturing
Jmp
Project Management
Program Management
Lean Manufacturing
R&D
Technical Leadership
Product Innovation
Engineering Management
Product Development
Cross Functional Team Leadership
Process Engineering
Engineering
Continuous Improvement
Software Engineering
Manufacturing
Jmp
Project Management
Program Management
Lean Manufacturing
R&D
Technical Leadership
Product Innovation
Engineering Management