Resumes
Resumes
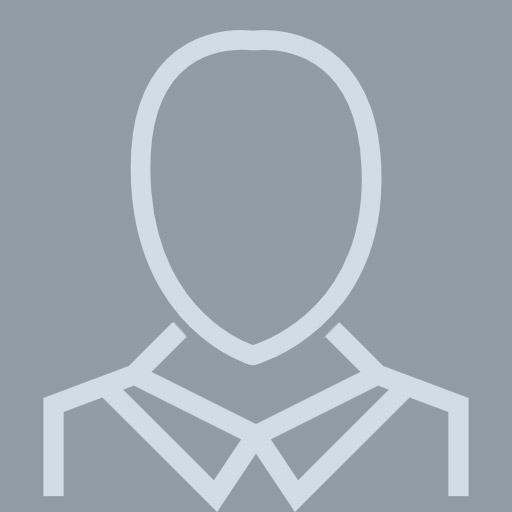
Associate Director
View pageLocation:
Duluth, MN
Industry:
Education Management
Work:
Natural Resources Research Insitute University of Mn
Associate Director
University of Minnesota Jan 2000 - Dec 2015
Director, Center For Applied Research and Technology Development
Steel Profitability Consulting Jan 1999 - Dec 2012
President
Inland Steel Company Jan 1996 - Jan 1998
Project Manager, Strip Casting Development
Inland Steel Company Jan 1994 - Jan 1996
Leader, Integrated Yield Lead Team
Associate Director
University of Minnesota Jan 2000 - Dec 2015
Director, Center For Applied Research and Technology Development
Steel Profitability Consulting Jan 1999 - Dec 2012
President
Inland Steel Company Jan 1996 - Jan 1998
Project Manager, Strip Casting Development
Inland Steel Company Jan 1994 - Jan 1996
Leader, Integrated Yield Lead Team
Education:
Missouri University of Science and Technology 1995 - 1995
Missouri University of Science and Technology 1978 - 1978
Missouri Science and Technology University 1975 - 1978
Columbia Engineering 1974 - 1975
Master of Science, Masters, Engineering Columbia University In the City of New York 1975 - 1975
Columbia University In the City of New York 1974 - 1974
Columbia University 1972 - 1974
Bachelors, Bachelor of Science, Engineering Macmurray College 1969 - 1972
Bachelors, Bachelor of Science, Engineering, Chemistry
Missouri University of Science and Technology 1978 - 1978
Missouri Science and Technology University 1975 - 1978
Columbia Engineering 1974 - 1975
Master of Science, Masters, Engineering Columbia University In the City of New York 1975 - 1975
Columbia University In the City of New York 1974 - 1974
Columbia University 1972 - 1974
Bachelors, Bachelor of Science, Engineering Macmurray College 1969 - 1972
Bachelors, Bachelor of Science, Engineering, Chemistry
Skills:
Leadership
Renewable Energy
Strategic Planning
Research
Project Management
Process Engineering
Energy
Engineering
Business Strategy
Environmental Awareness
Microsoft Office
Public Speaking
Sustainability
Mining
Business Development
Continuous Improvement
Minerals
Contract Negotiation
Project Planning
Strategy
Business Planning
Entrepreneurship
Metallurgy
Cleantech
Program Management
Contract Management
Management Consulting
Raw Materials
Renewable Energy
Strategic Planning
Research
Project Management
Process Engineering
Energy
Engineering
Business Strategy
Environmental Awareness
Microsoft Office
Public Speaking
Sustainability
Mining
Business Development
Continuous Improvement
Minerals
Contract Negotiation
Project Planning
Strategy
Business Planning
Entrepreneurship
Metallurgy
Cleantech
Program Management
Contract Management
Management Consulting
Raw Materials
Interests:
Recycling and Remediation
Secondary Wood Products
Education
Applied Research and Development
Forestry
Mineral and Metals Processing
Renewable Energy
Secondary Wood Products
Education
Applied Research and Development
Forestry
Mineral and Metals Processing
Renewable Energy
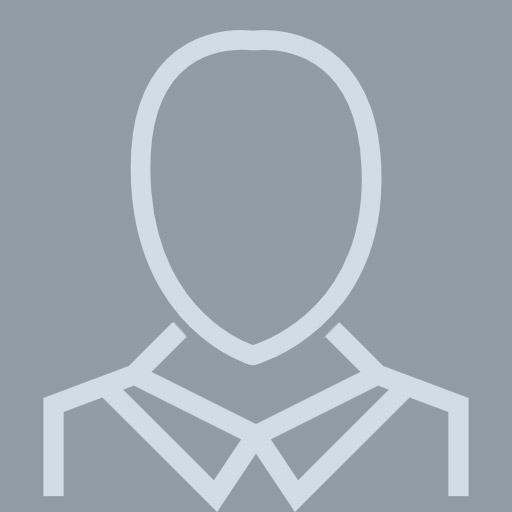
Director
View pageLocation:
4214 Glen Oaks Dr, Crown Point, IN 46307
Industry:
Mining & Metals
Work:
Natural Resources Research Institute
Director
Director