Resumes
Resumes
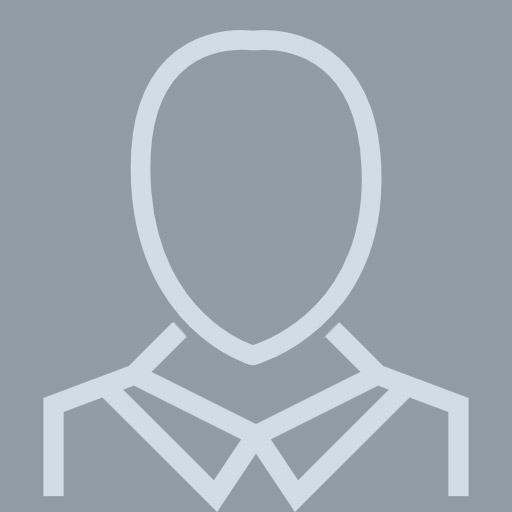
Head, Renewable And Alternative Feedstocks Development
View pageLocation:
Pittsburgh, PA
Industry:
Chemicals
Work:
Bayer Materialscience
Senior Mgr, Technology Development and University Engagement
Bayer Materialscience
Head, Renewable and Alternative Feedstocks Development
Bayer Materialscience Jan 2004 - Dec 2011
Process Development Manager
Lyondellbasell 1991 - 2000
Technology Manager
Arco Chemical Company 1997 - 1998
Technology Manager
Senior Mgr, Technology Development and University Engagement
Bayer Materialscience
Head, Renewable and Alternative Feedstocks Development
Bayer Materialscience Jan 2004 - Dec 2011
Process Development Manager
Lyondellbasell 1991 - 2000
Technology Manager
Arco Chemical Company 1997 - 1998
Technology Manager
Education:
Massachusetts Institute of Technology Sep 1983 - Sep 1987
Doctorates, Doctor of Philosophy, Chemical Engineering Massachusetts Institute of Technology 1981 - 1982
University of Wisconsin - Madison 1978 - 1981
Bachelors, Bachelor of Science, Chemical Engineering University of Wisconsin - Milwaukee 1977 - 1978
Doctorates, Doctor of Philosophy, Chemical Engineering Massachusetts Institute of Technology 1981 - 1982
University of Wisconsin - Madison 1978 - 1981
Bachelors, Bachelor of Science, Chemical Engineering University of Wisconsin - Milwaukee 1977 - 1978
Skills:
Polymers
Chemical Engineering
R&D
Chemistry
Process Engineering
Polyurethane
Process Simulation
Process Optimization
Catalysis
Coatings
Plastics
Materials Science
Technology Transfer
Leadership
Materials
Manufacturing
Commercialization
Chemical Industry
Characterization
Research and Development
Polymer Chemistry
Process Safety
Market Development
Nanotechnology
Organic Chemistry
Polymer Science
Extrusion
Raw Materials
Adhesives
Design of Experiments
Formulation
Chemical Engineering
R&D
Chemistry
Process Engineering
Polyurethane
Process Simulation
Process Optimization
Catalysis
Coatings
Plastics
Materials Science
Technology Transfer
Leadership
Materials
Manufacturing
Commercialization
Chemical Industry
Characterization
Research and Development
Polymer Chemistry
Process Safety
Market Development
Nanotechnology
Organic Chemistry
Polymer Science
Extrusion
Raw Materials
Adhesives
Design of Experiments
Formulation
Interests:
Social Services