Professional Records
License Records
David John Wadas
Address:
Portage, MI 49002
License #:
DS028888L - Expired
Category:
Dentistry
Type:
Dentist
Medicine Doctors
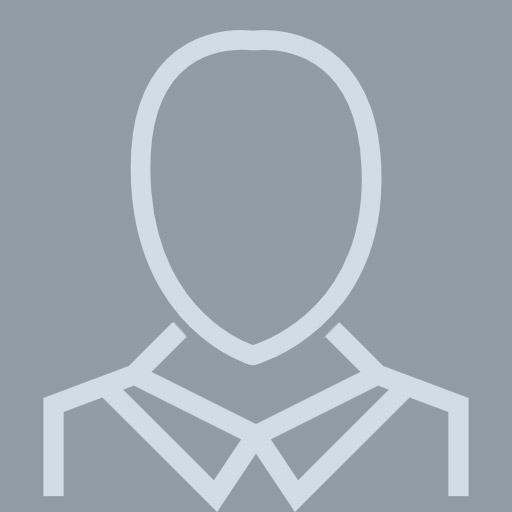
Dr. David J Wadas, Portage MI - DDS (Doctor of Dental Surgery)
View pageSpecialties:
Dentistry
Address:
636 E Milham Ave, Portage, MI 49002
(269) 323-1802 (Phone), (269) 323-1940 (Fax)
(269) 323-1802 (Phone), (269) 323-1940 (Fax)
Languages:
English