Resumes
Resumes
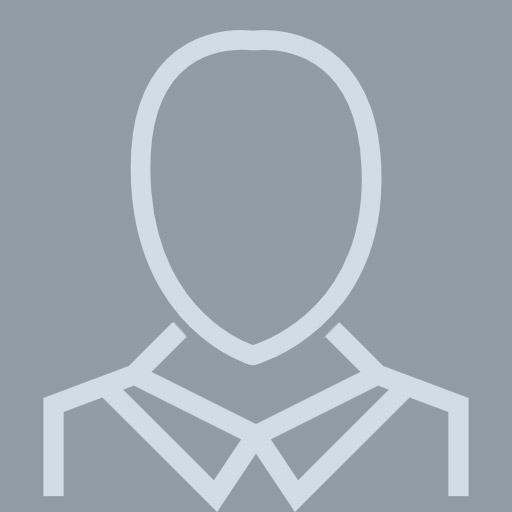
Process Development Engineer
View pageLocation:
Canandaigua, NY
Industry:
Electrical/Electronic Manufacturing
Work:
Zotos International (Subsidiary of Shiseido Usa)
Process Development Engineer
Thomas Electronics Jun 2014 - Dec 2014
Chemical Process Engineer
Ferro Corporation Sep 2007 - Jun 2014
Research and Development Process Engineering Technician Iv
Ferro Corporation Aug 2006 - Sep 2007
Chemical Mechanical Polishing Technician Iv
Ferro Corporation Jun 2004 - Aug 2006
Manufacturing Engineer
Process Development Engineer
Thomas Electronics Jun 2014 - Dec 2014
Chemical Process Engineer
Ferro Corporation Sep 2007 - Jun 2014
Research and Development Process Engineering Technician Iv
Ferro Corporation Aug 2006 - Sep 2007
Chemical Mechanical Polishing Technician Iv
Ferro Corporation Jun 2004 - Aug 2006
Manufacturing Engineer
Education:
Rochester Institute of Technology 2000 - 2003
Master of Science, Masters, Materials Science, Engineering Rochester Institute of Technology 1997 - 2000
Bachelors, Bachelor of Science, Chemistry State University of New York at Fredonia 1989 - 1993
Bachelors, Teaching, Elementary Education
Master of Science, Masters, Materials Science, Engineering Rochester Institute of Technology 1997 - 2000
Bachelors, Bachelor of Science, Chemistry State University of New York at Fredonia 1989 - 1993
Bachelors, Teaching, Elementary Education
Skills:
Chemistry
Manufacturing
Product Development
Continuous Improvement
Coatings
Materials Science
Process Engineering
Process Improvement
Lean Manufacturing
Iso 9000
Quality System
Root Cause Analysis
Process Optimization
Materials
Iso
Engineering
Characterization
Polymers
Spc
Cross Functional Team Leadership
Design of Experiments
Formulation
Screen Printing
Quality Improvement
Microsoft Office
Semiconductor Process
Clean Rooms
Research and Development
Statistical Process Control
Six Sigma
Manufacturing
Product Development
Continuous Improvement
Coatings
Materials Science
Process Engineering
Process Improvement
Lean Manufacturing
Iso 9000
Quality System
Root Cause Analysis
Process Optimization
Materials
Iso
Engineering
Characterization
Polymers
Spc
Cross Functional Team Leadership
Design of Experiments
Formulation
Screen Printing
Quality Improvement
Microsoft Office
Semiconductor Process
Clean Rooms
Research and Development
Statistical Process Control
Six Sigma
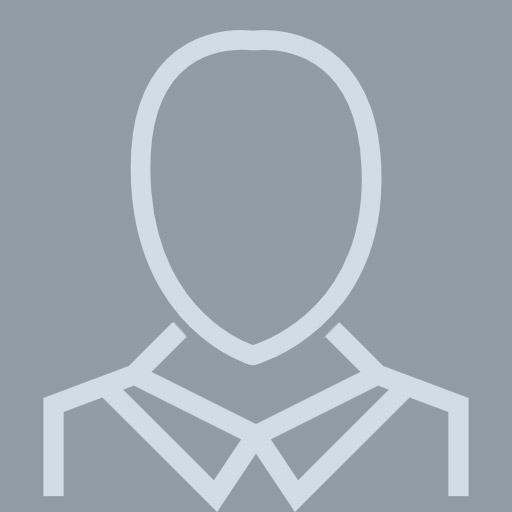
David Tysiac Canandaigua, NY
View pageWork:
Thomas Electronics
Clyde, NY
Jun 2014 to Dec 2014
Process Engineer
Ferro Electronic Materials
Penn Yan, NY
Sep 2007 to Jun 2014
Engineering Technician IV
Chemical Mechanical Planarization Research & Development Lab
Aug 2006 to Sep 2007
Chemical Mechanical Polishing Technician IV
Solids of Cerium Slurry
Jun 2004 to Aug 2006
Manufacturing Engineer
Chemical Mechanical Planarization Research & Development Lab
Jan 2004 to Jun 2004
Research Scientist II
Chemical Mechanical Planarization Research & Development Lab
Jul 2000 to Jan 2004
Chemical Mechanical Polishing Technician IV
Eastman Kodak Company
Rochester, NY
Aug 1998 to Jul 2000
Clyde, NY
Jun 2014 to Dec 2014
Process Engineer
Ferro Electronic Materials
Penn Yan, NY
Sep 2007 to Jun 2014
Engineering Technician IV
Chemical Mechanical Planarization Research & Development Lab
Aug 2006 to Sep 2007
Chemical Mechanical Polishing Technician IV
Solids of Cerium Slurry
Jun 2004 to Aug 2006
Manufacturing Engineer
Chemical Mechanical Planarization Research & Development Lab
Jan 2004 to Jun 2004
Research Scientist II
Chemical Mechanical Planarization Research & Development Lab
Jul 2000 to Jan 2004
Chemical Mechanical Polishing Technician IV
Eastman Kodak Company
Rochester, NY
Aug 1998 to Jul 2000
Education:
Rochester Institute of Technology
Rochester, NY
2003
Masters of Science in Material Science and Engineering
Rochester Institute of Technology
Rochester, NY
2000
Bachelor of Science in Chemistry
SUNY Fredonia
Fredonia, NY
1993
Bachelor of Science in Elementary Education
Conductivity & Polymerization of Poly
Rochester, NY
2003
Masters of Science in Material Science and Engineering
Rochester Institute of Technology
Rochester, NY
2000
Bachelor of Science in Chemistry
SUNY Fredonia
Fredonia, NY
1993
Bachelor of Science in Elementary Education
Conductivity & Polymerization of Poly