Resumes
Resumes
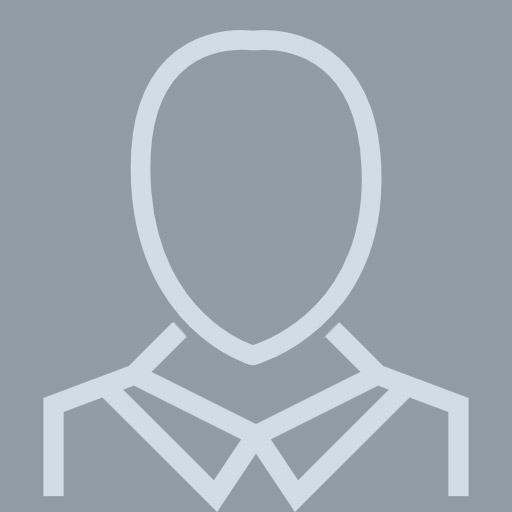
Research And Development Engineer
View pageLocation:
5402 Lynx St, Frederick, CO 80504
Industry:
Mechanical Or Industrial Engineering
Work:
Covidien
Research and Development Engineer
Parker Hannifin Oct 2014 - Sep 2015
Product Engineer
Parker Hannifin May 2013 - Oct 2014
Vessel Design Engineer
Ptc Oct 2011 - May 2013
Applications Engineer
Hunter Douglas May 2011 - Sep 2011
Process Engineering Intern
Research and Development Engineer
Parker Hannifin Oct 2014 - Sep 2015
Product Engineer
Parker Hannifin May 2013 - Oct 2014
Vessel Design Engineer
Ptc Oct 2011 - May 2013
Applications Engineer
Hunter Douglas May 2011 - Sep 2011
Process Engineering Intern
Education:
Colorado State University 2006 - 2011
Bachelors, Mechanical Engineering
Bachelors, Mechanical Engineering
Skills:
Cad
Mechanical Engineering
Mathcad
Design For Manufacturing
Pro Engineer
Finite Element Analysis
Design Engineering
Batteries
Machining
Autodesk Inventor
Ptc Creo
Engineering Drawings
Unigraphics
Windchill
Mechanical Engineering
Mathcad
Design For Manufacturing
Pro Engineer
Finite Element Analysis
Design Engineering
Batteries
Machining
Autodesk Inventor
Ptc Creo
Engineering Drawings
Unigraphics
Windchill
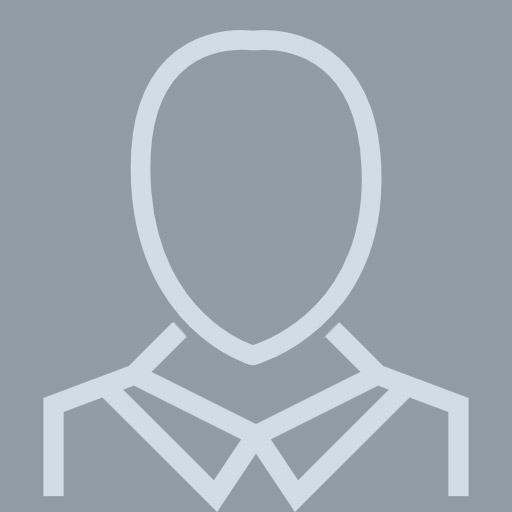
Curtis Siebenaller Fort Collins, CO
View pageWork:
PTC
Oct 2011 to 2000
Application Engineer
Hunter Douglas, Inc.
Broomfield, CO
May 2011 to Sep 2011
Process Engineering Intern
Colorado State University Bookstore
Fort Collins, CO
Jan 2009 to May 2011
Customer Service Student Manager
Hunter Douglas, Inc.
Broomfield, CO
Jun 2008 to Jul 2008
Hourly Production Employee
Oct 2011 to 2000
Application Engineer
Hunter Douglas, Inc.
Broomfield, CO
May 2011 to Sep 2011
Process Engineering Intern
Colorado State University Bookstore
Fort Collins, CO
Jan 2009 to May 2011
Customer Service Student Manager
Hunter Douglas, Inc.
Broomfield, CO
Jun 2008 to Jul 2008
Hourly Production Employee
Education:
Colorado State University
Fort Collins, CO
Jan 2006 to Jan 2011
BS in Mechanical Engineering
Fort Collins, CO
Jan 2006 to Jan 2011
BS in Mechanical Engineering
Skills:
Compurter Aided Design, Mathematical Design, PTC Technical Support, Machine Production, Machine Maintenance, MS Office Suite