Resumes
Resumes
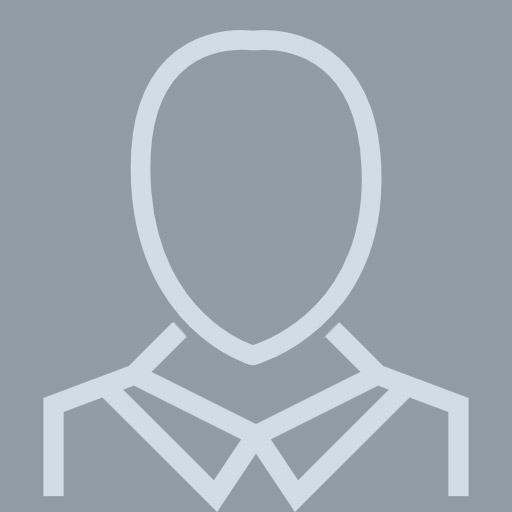
Engineering And Product Development Executive
View pagePosition:
R&D Enginering Director at Trimble Navigation
Location:
Corvallis, Oregon Area
Industry:
Computer Hardware
Work:
Trimble Navigation - Corvallis, Oregon Area since Dec 2011
R&D Enginering Director
nLight Sep 2009 - Dec 2011
Director of Laser Systems Integration
Deep Photonics Corporation Jan 2006 - Sep 2009
Vice President of Engineering
ATS Automation Tooling Systems Oct 2003 - Jan 2006
Operations Manager
Electroglas Inspection Products Dec 1997 - Jun 2003
Vice President of Engineering
R&D Enginering Director
nLight Sep 2009 - Dec 2011
Director of Laser Systems Integration
Deep Photonics Corporation Jan 2006 - Sep 2009
Vice President of Engineering
ATS Automation Tooling Systems Oct 2003 - Jan 2006
Operations Manager
Electroglas Inspection Products Dec 1997 - Jun 2003
Vice President of Engineering
Skills:
Semiconductors
Automation
Product Development
Embedded Systems
Engineering Management
Manufacturing
Electronics
R&D
Automation
Product Development
Embedded Systems
Engineering Management
Manufacturing
Electronics
R&D
Certifications:
Instrument Rated Private Pilot, Federal Aviation Administration (FAA)
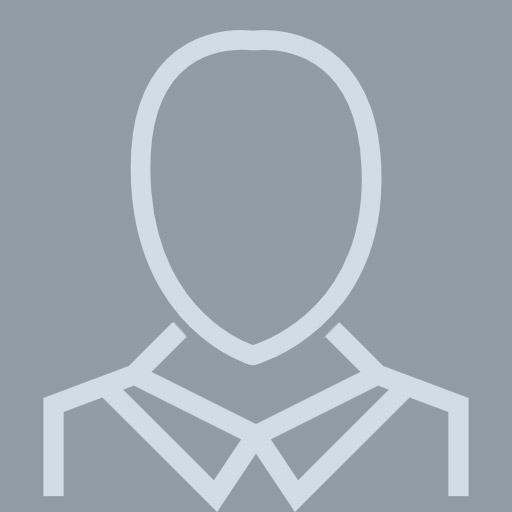
Engineering And Project Management Director
View pageLocation:
2556 northwest Skyline Ter, Albany, OR 97321
Industry:
Wireless
Work:
Trimble
Engineering and Project Management Director
Nlight Sep 2009 - Dec 2011
Director of Laser Systems Integration
Deep Photonics Corporation Jan 2006 - Sep 2009
Vice President of Engineering
Ats Automation Oct 2003 - Jan 2006
Operations Manager
Electroglas Dec 1997 - Jun 2003
Vice President of Engineering
Engineering and Project Management Director
Nlight Sep 2009 - Dec 2011
Director of Laser Systems Integration
Deep Photonics Corporation Jan 2006 - Sep 2009
Vice President of Engineering
Ats Automation Oct 2003 - Jan 2006
Operations Manager
Electroglas Dec 1997 - Jun 2003
Vice President of Engineering
Education:
University of the Pacific 1983 - 1988
Bachelors, Bachelor of Science In Electrical Engineering, Electrical Engineering, Physics
Bachelors, Bachelor of Science In Electrical Engineering, Electrical Engineering, Physics
Skills:
Engineering Management
Product Development
Electronics
Semiconductors
Automation
Manufacturing
Embedded Systems
Testing
Engineering
Cross Functional Team Leadership
R&D
Integration
Product Management
Start Ups
Management
Robotics
Process Improvement
Software Documentation
Programming
Lean Manufacturing
Software Development
Software Engineering
Systems Engineering
System Architecture
Continuous Improvement
Troubleshooting
Optics
Quality Assurance
Product Design
Product Development
Electronics
Semiconductors
Automation
Manufacturing
Embedded Systems
Testing
Engineering
Cross Functional Team Leadership
R&D
Integration
Product Management
Start Ups
Management
Robotics
Process Improvement
Software Documentation
Programming
Lean Manufacturing
Software Development
Software Engineering
Systems Engineering
System Architecture
Continuous Improvement
Troubleshooting
Optics
Quality Assurance
Product Design
Interests:
Science and Technology
Children
Arts and Culture
Children
Arts and Culture
Certifications:
Instrument Rated Private Pilot