Resumes
Resumes
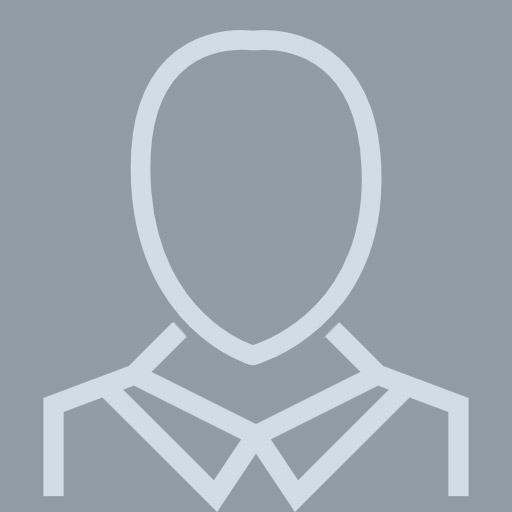
Owner
View pageLocation:
Lakeland, FL
Industry:
Research
Work:
Jdc of Oregon
Owner
Owner
Education:
Oregon State University 1964 - 1975
Skills:
Start Ups
Business Strategy
Product Development
Entrepreneurship
New Business Development
Strategic Planning
Management Consulting
Business Strategy
Product Development
Entrepreneurship
New Business Development
Strategic Planning
Management Consulting
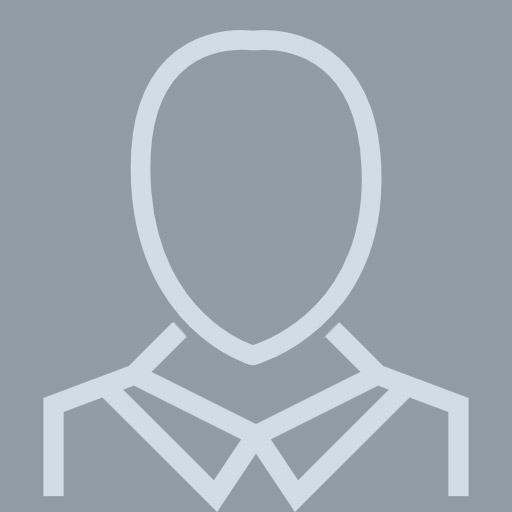
Chairman
View pageLocation:
Pasco, WA
Industry:
Research
Work:
Jdcphosphate, Inc
Chairman
Chairman
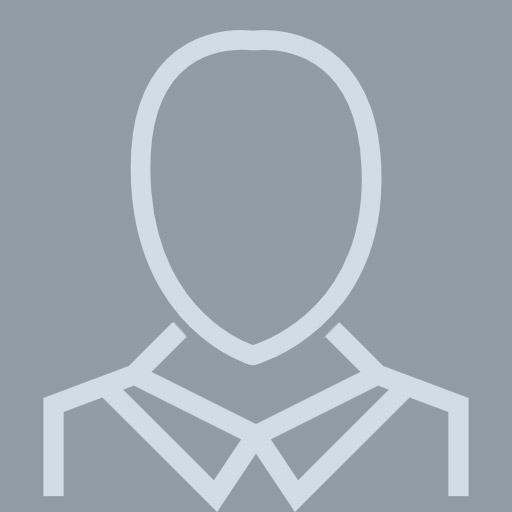
Cto At Jdcphosphate
View pagePosition:
cto at jdcphosphate
Location:
Richland/Kennewick/Pasco, Washington Area
Industry:
Research
Work:
jdcphosphate
cto
jamegy Inc Jan 1988 - Mar 2002
president
cto
jamegy Inc Jan 1988 - Mar 2002
president
Education:
Oregon State University 1963 - 1975
PhD, Chemistry-Chem Engineering
PhD, Chemistry-Chem Engineering